A common principle in Operational Qualification (OQ) studies is to challenge processes under worst case conditions. A "worst case" condition or set of conditions are generally those parameters encompassing the upper and lower processing limits for a process and circumstances, within SOPs or batch records, which pose the greatest chance of product or process failure when compared to nominal conditions. Such conditions do not necessarily include product or process failure.
The primary elements of process validation are:
- Installation Qualification (IQ)
- Operational Qualification (OQ)
- Performance Qualification (PQ)
Other elements of process validation include:
- Test or analytical Method Validation (TMV)
- Software Validation (SWV)
- Construction Qualification, where applicable
Together, a process validation strategy may resemble the following:
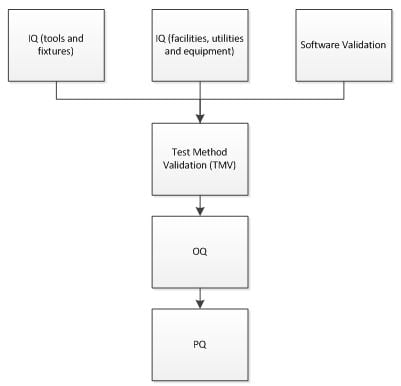
A common mistake in the OQ phase of a Process Validation (PV) approach or strategy is to not adequately identify and therefore not test actual worst case conditions. Many times, the study design will limit itself to a single condition, e.g., upper and lower dispensing volumes during a fill and finish operation. The following list includes many factors that are commonly overlooked but have influences on process variability.
- Equipment capability
- Equipment calibration and tooling
- Ramp up times/storage times
- Influence of diverse lots of components and raw materials
- Influence of aging/shelf life of components and raw materials
- Influence of different suppliers of the same or equivalent components and raw materials
- Manufacturing conditions and environment
- Influence of different operators on different shifts
Taking the broad array of other influences into account, the following points provide guidance on how to determine what the real worst case conditions may be.
- Prepare a list of every process step by name in sequential manufacturing order. Include all manufacturing, testing and inspection steps.
- Convert the list to a process map or flow diagram.
- Identify the specifications as per the process parameters of all individual processes. A matrix approach may be helpful.

- Use pFMEA methods and techniques to identify and understand critical process parameters
- Use Design of Experiments (DOE) to determine process parameter and/or optimum setting variability.
- Establish a statistically valid sampling plan to ensure the quantity of product to be tested is based on a sound and defendable rationale.
Learn more about ProPharma's Process Validation services. Contact us to get in touch with our subject matter experts for a customized Compliance presentation.