commissioning, qualification, & validation (CQV)
ProPharma has more than two decades of experience commissioning, qualifying, and validating (CQV) manufacturing facilities and processes for regulated clients.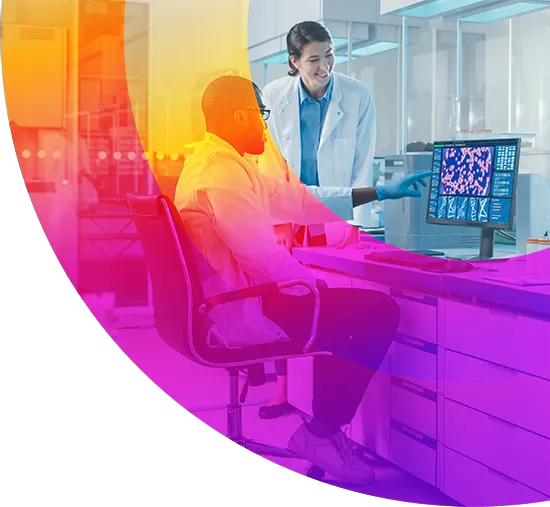
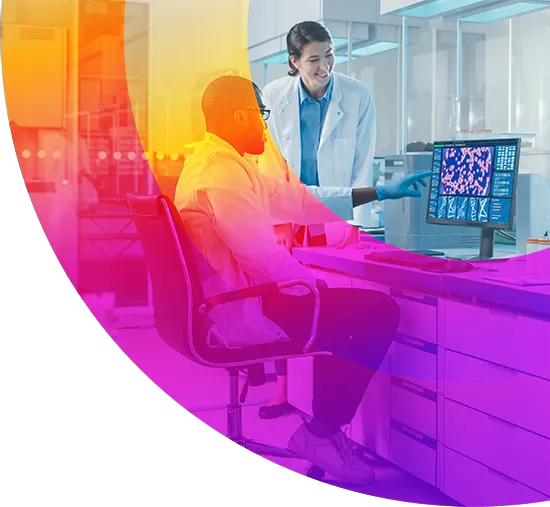
+3,500
Projects Executed
+650
Clients Supported
17 years
Average Staff Experience
+40%
Clients we've supported for over a decade
Industry-leading, Full-Service CQV
We apply our expertise with a risk-based approach to help our clients reach their project goals. Our expert CQV consultants also understand that although this approach can be helpful in minimizing cost and labor, each project is different and requires a tailored approach. Our project managers and subject matter experts have experience working with the different functional teams within manufacturing, validation, and quality to help define the best solution for our clients. The size and strength of ProPharma allows us to rapidly mobilize and demobilize project teams to meet schedule requirements
Why is CQV Important?
Commissioning, Qualification, and Validation (CQV) are essential processes in regulated industries, ensuring compliance, product quality, and safety. They mitigate risks, maintain data integrity, improve efficiency, and support regulatory approvals. CQV also enhances reputation, saves costs, and prioritizes patient safety in healthcare.
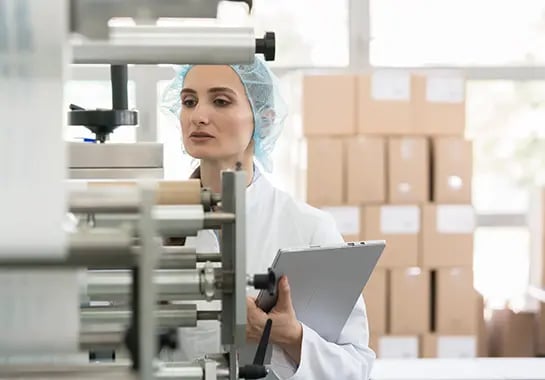
Our Commissioning, Qualification, & Validation Services
Validation Program Development
We partner with organizations to develop and implement continuously reliable and compliant validation programs that help clients successfully bring products to market. ProPharma utilizes a scalable/flexible approach to ensure the validation program is right-sized based on clients’ industry, clinical/commercial stage and size.
Gap
Assessments
Our gap assessment process utilizes a planning, execution, and reporting format focused on identifying program gaps and recommended corrective action/remediation.
Facility, Equipment, & Utility Qualifications
Projects ranging in size from small system qualifications to full greenfield/brownfield facility buildouts are routine. Our in-house project managers and SMEs have vast industry experience, transferring knowledge and expertise to the project team to ensure a seamless and efficient approach. Whether it is a single project or a portfolio of CapEx / OpEx projects at a single site, we are built to execute successfully.
Cleaning & Sterilization Validation
Our sterilization services include the physical (IQ and OQ) and microbiological inactivation (PQ) testing aspects for steam sterilization, dry heat, and vaporized hydrogen peroxide.
Our cleaning services involve a defined clustering approach of products, protocols, defined assays and limits, protocol writing, in-test lab selection support, execution of testing support, and reporting that results in effective controls for limiting the bioburden.
Process Validation
ProPharma’s product lifecycle approach towards process validation in pharmaceuticals and biotech helps you deliver optimal product quality by identifying the presence and degree of process variation and the impact variation has on process efficiency and product quality. Minimizing the variation reduces risks and ensures a robust process that reliably produces quality product.
Project Management
Through its internal project management process, ProPharma provides full oversight for validation services or capital project management outsourcing. ProPharma has successfully executed thousands of C&Q projects over the last 20+ years providing various levels of project management focused on schedule, cost, communication, and conflict management.
Staff Support & Outsourcing
At ProPharma, our network of 1,000+ CQV professionals can augment your internal capabilities to ensure project timelines are met utilizing experienced professionals. Our team acts as an extension of your engineering/quality/validation department, while our management team provides you with a direct line of communication for any operational assistance related to the resources deployed.
“Lyell engaged ProPharma as our validation partner as we built and qualified the LyFE Manufacturing Center. ProPharma assisted in all phases of the qualification including establishing the facility and equipment qualification program, protocol generation, protocol execution, and writing the final reports. They played a critical role in getting the facility ready on time and on budget to support the Lyell clinical trials.”
David Shank - Lyell Immunopharma, Inc.
Vice President, Manufacturing
“Lyell engaged ProPharma as our validation partner as we built and qualified the LyFE Manufacturing Center. ProPharma assisted in all phases of the qualification including establishing the facility and equipment qualification program, protocol generation, protocol execution, and writing the final reports. They played a critical role in getting the facility ready on time and on budget to support the Lyell clinical trials.”
David Shank - Lyell Immunopharma, Inc.
Vice President, Manufacturing
Expert Solutions. Proven Results.
With all clients, we take a balanced, risk-based approach to deliver the most current, relevant, and value-added services and recommendations so they can achieve their regulatory compliance and quality assurance goals efficiently and effectively.
FDA & ISO Experience
We have in-depth knowledge of 21CFR Parts 210, 211, 11, & 820 and ISO13485.
Industry Standards & Best Practices
Flexible Approach
Right-Sized Solutions
We provide tailored CQV-related policies and procedures to clients at the level of equipment usage and related regulatory and business risk they need.
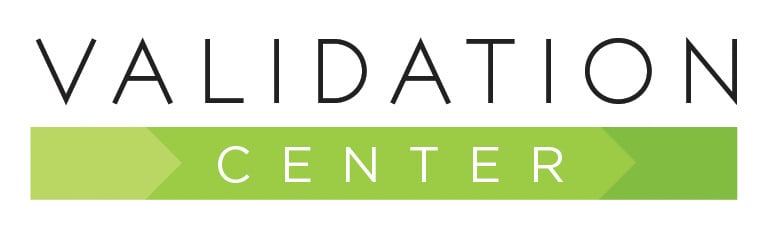
CQV Training & Resources
Access essential training and resources for computer system validation, compliance, and data integrity at Validation Center, a ProPharma knowledge center and resource.
Attend free webinars, enroll in online and in-person classes in the US and Europe, and download valuable templates and standard operating procedures. Validation Center offers everything you need for CQV and software quality assurance.
Meet our CQV Experts & Consultants
-
Kyle Nordstrom
Vice President, Compliance & Quality Assurance
-
John Ryan
Senior Director, CQV Expert
-
Todd Sevier
Associate Director, CQV Expert
-
Jaime Vaquer-Morales
Senior Project Manager, Cleaning Validation Expert
-
TJ Stough
Senior Project Manager, Sterilization Expert
-
Fred Wiles
Principal Consultant, Process Validation Expert
Kyle Nordstrom
John Ryan
Todd Sevier
Jaime Vaquer-Morales
TJ Stough
Fred Wiles
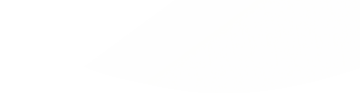
Customized Strategy. Globally Scaled Solutions.
With offices and compliance consultants located around the world, ProPharma offers the capability to execute CQV projects / support in different GxP areas on a global scale, creating efficiency and savings.
News & Insights
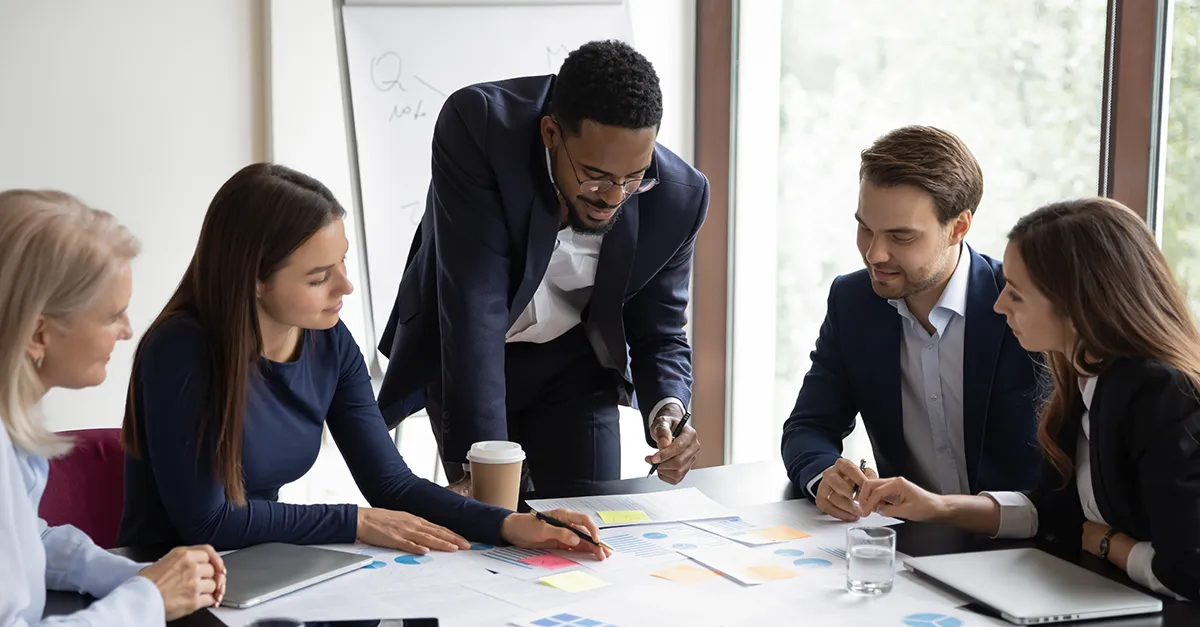
June 24, 2025
Maximizing the Value of FDA Pre-IND Meetings for Successful 505(b)(2) NDA Submissions
Learn how to prepare for FDA Pre-IND meetings to streamline 505(b)(2) NDA submissions and avoid costly delays with expert regulatory strategies.
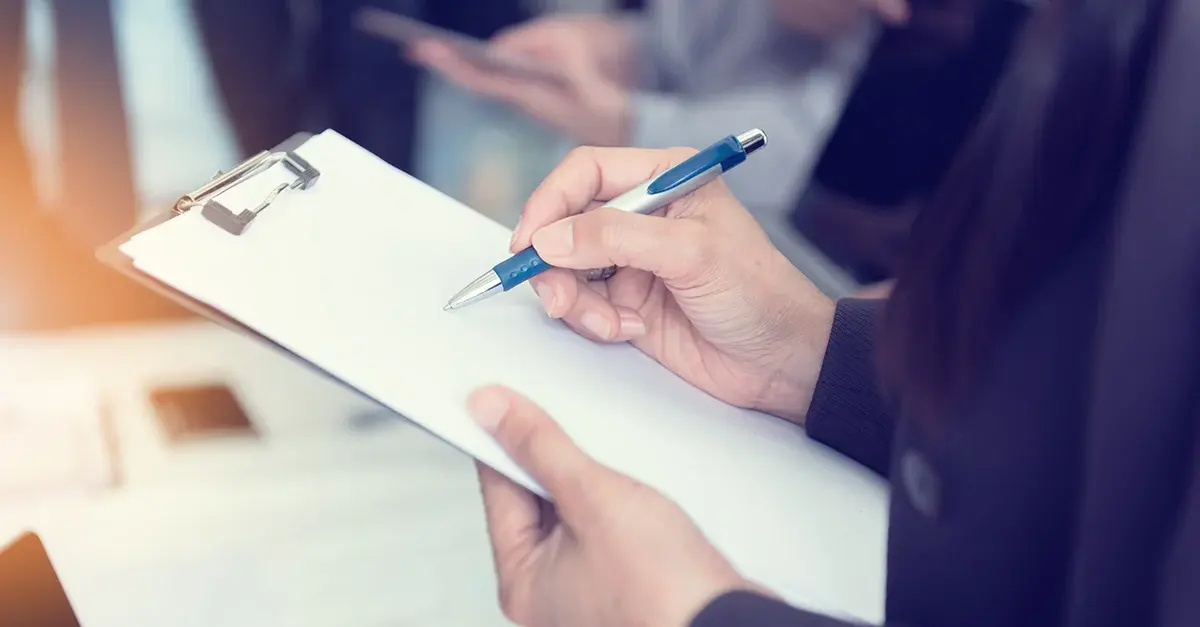
June 23, 2025
The Joint Commission Adds Pharmacists to Survey Teams: A Step Towards Comprehensive Healthcare Quality
The Joint Commission's inclusion of pharmacists in survey teams enhances medication safety, clinical outcomes, and promotes comprehensive care in healthcare facilities.
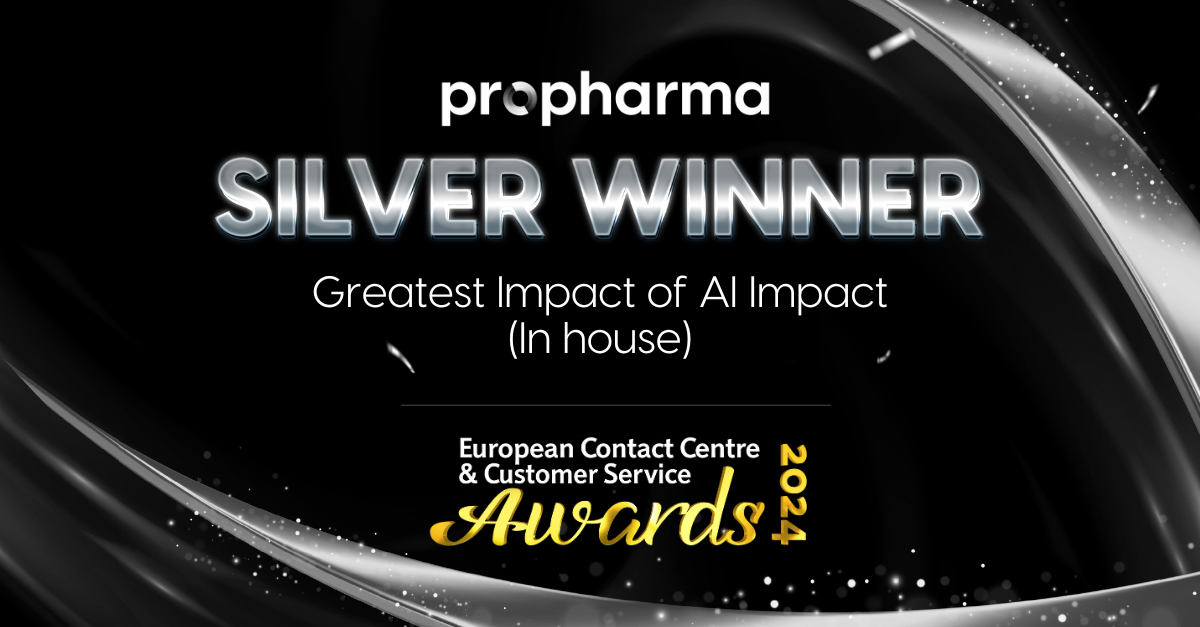
January 31, 2025
ProPharma Recognized for AI Excellence at ECCCSA
ProPharma wins Silver at ECCCSA for AI innovation in Medical Information, enhancing efficiency and quality in delivering accurate medical information.
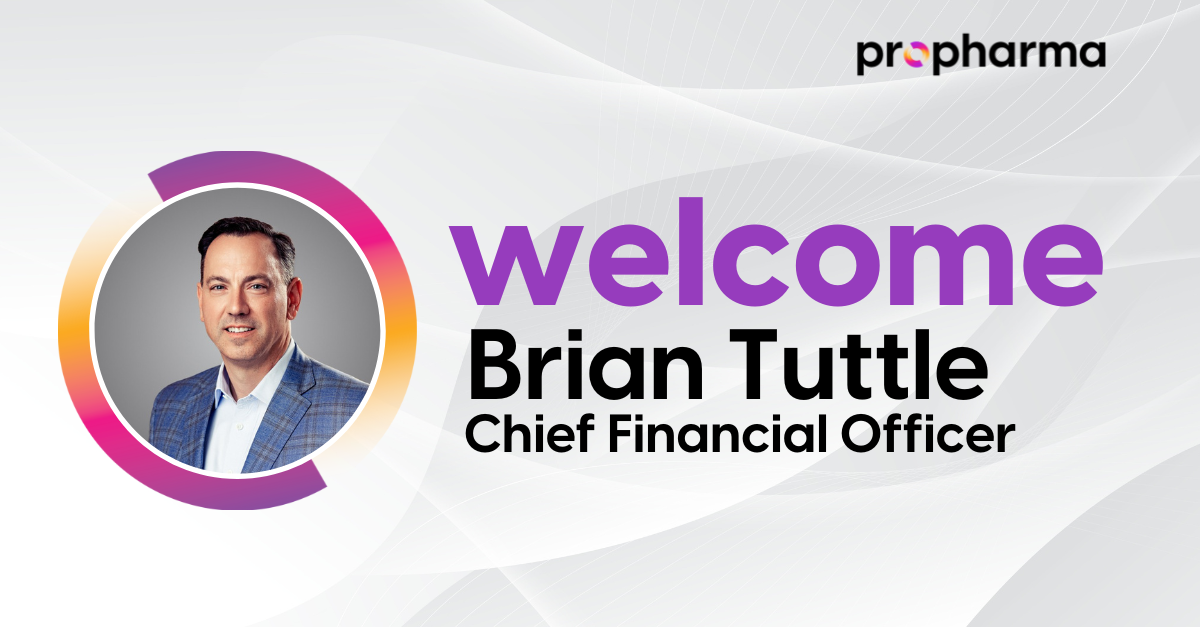
October 21, 2024
ProPharma Appoints Brian Tuttle as Chief Financial Officer
ProPharma appoints Brian Tuttle as CFO to drive financial strategy and accelerate global growth, leveraging his 20 years of life sciences industry experience.
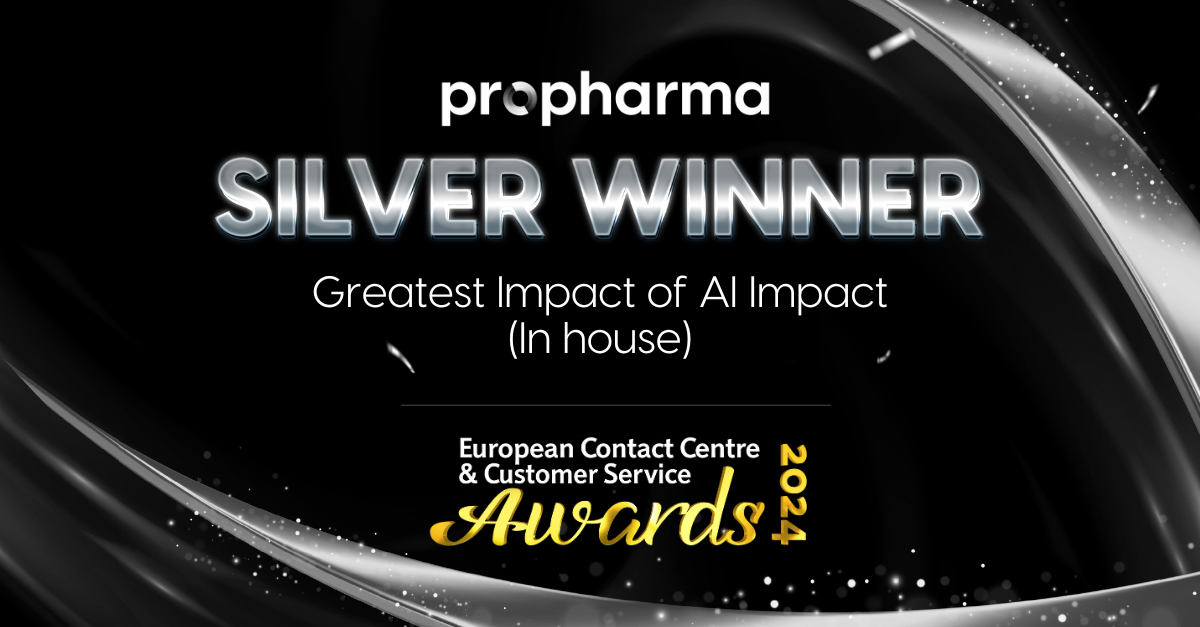
January 31, 2025
ProPharma Recognized for AI Excellence at ECCCSA
ProPharma wins Silver at ECCCSA for AI innovation in Medical Information, enhancing efficiency and quality in delivering accurate medical information.
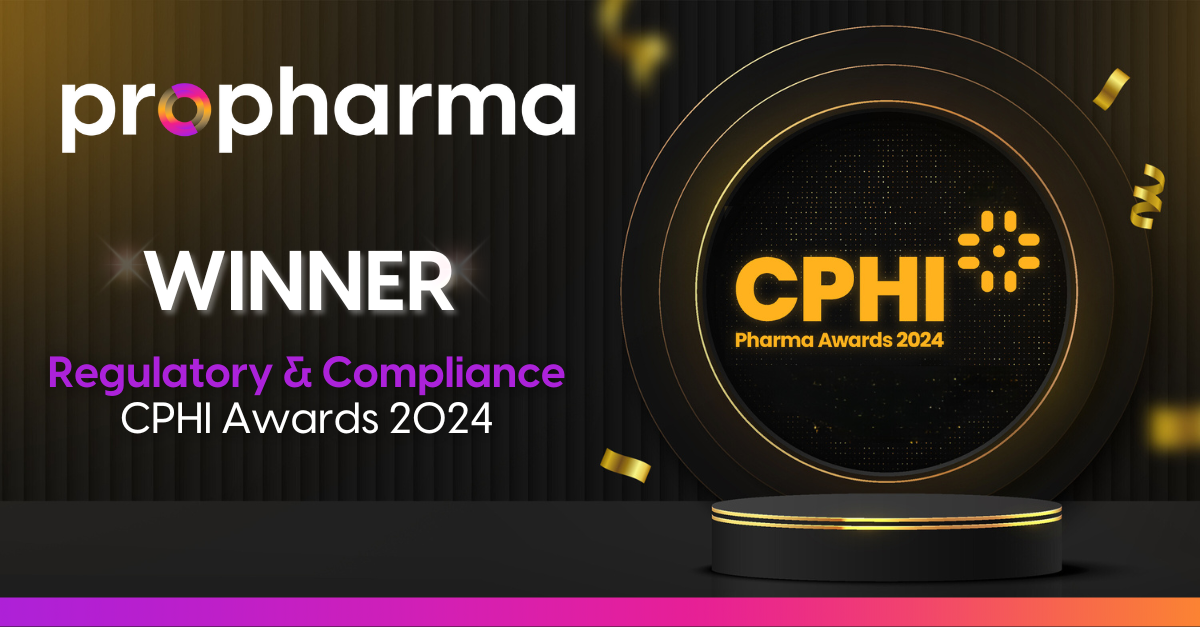
October 9, 2024
ProPharma Receives 2024 CPHI Regulatory and Compliance Award
ProPharma wins CPHI Pharma Award for excellence in regulatory and compliance innovation, enhancing efficiency and accelerating market access for life-saving therapies.
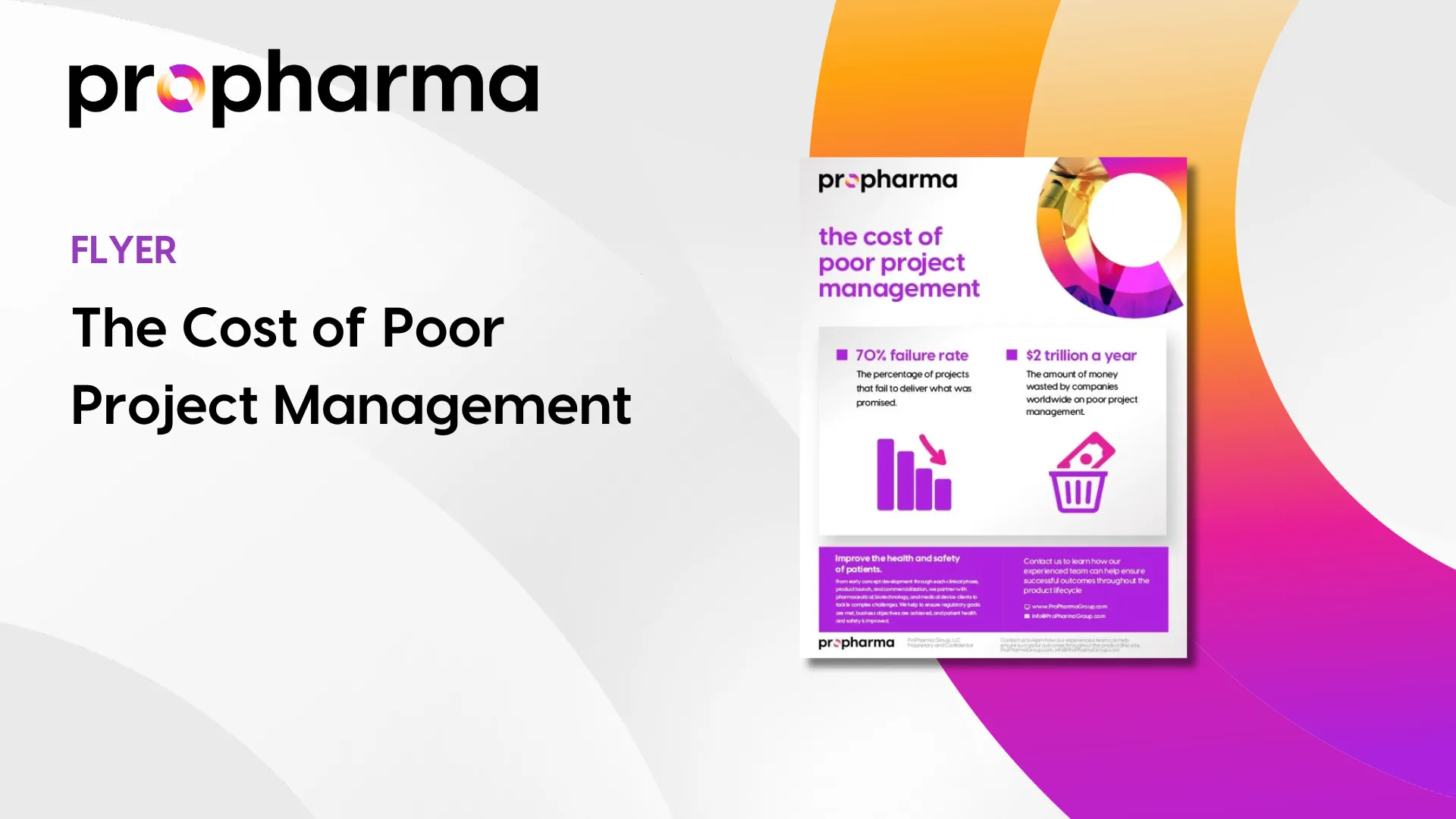
June 10, 2022
The Cost of Poor Project Management
Project Management isn’t for the faint of heart. There is a shockingly high rate of project failure… but on the other hand, great project management can be a key differentiator that leads a company...
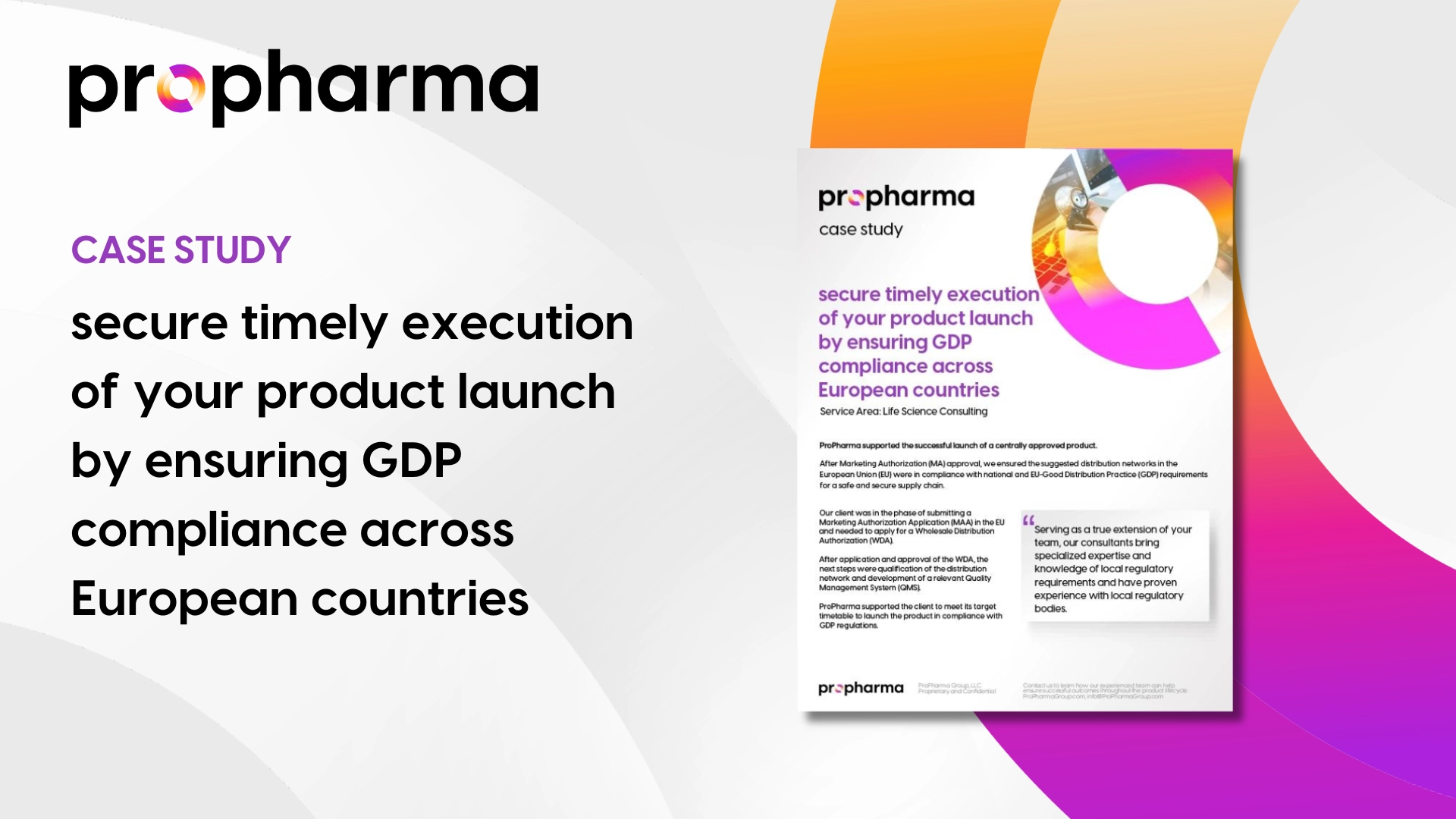
August 31, 2022
Successfully Passing MHRA Inspections for Overseas Manufacturing Sites
ProPharma offers GMP and GDP compliance services from clinical development to commercial distribution of the products' lifecycle. ProPharma’s Compliance and Quality team completed the first on-site...
News & Insights